

Polski przemysł skupiony w Grupie Kapitałowej PGZ z racji wielości programów modernizacyjnych na rzecz Sił Zbrojnych RP zawsze był ważną częścią tematów podejmowanych w miesięczniku „Nowa Technika Wojskowa”. Po inwazji Rosji na Ukrainę, dostawach polskiego sprzętu dla obrońców, planach strategicznych zakupów w przemyśle Korei Południowej – w bieżącym roku tych tematów jest nawet zdecydowanie więcej. Obszary nad którymi pracujemy od lat oraz te nowe, tegoroczne, wyjaśnia Prezes Zarządu PGZ S.A. Sebastian Chwałek w wywiadzie z redaktorem naczelnym miesięcznika „Nowa Technika Wojskowa” Mariuszem Cielmą.
Panie Prezesie, na początek prosiłbym o ocenę ostatniego roku dla PGZ i wchodzących w skład Grupy spółek?
Prezes Zarządu PGZ S.A. Sebastian Chwałek: Na pewno wiele mogliście państwo obserwować z zewnątrz, bo wiele naszych działań było widocznych w mediach, ale również fizycznie można zaobserwować zmianę. A jest widoczne duże przyspieszenie, jeśli chodzi o liczbę kontraktów, które mamy realizować dla polskich sił zbrojnych. Są to projekty, na które czekaliśmy wiele lat, ale są również i takie, które pojawiły się z uwagi na wojnę toczącą się za naszą wschodnią granicą. Ta bezprecedensowa napaść na Ukrainę dała również naszemu resortowi obrony obserwacje, które owocują w podejmowaniu decyzji wcześniej nierozważanych.
Możemy wymienić jakieś przykłady?
Na przykład w ramach programu Narew mamy „małą Narew”, która nie była wcześniej planowana, a wynikła po 24 lutego, z racji pilniejszego zabezpieczenia niektórych wojskowych potrzeb. Zapewne słyszał Pan o programie Pilica+. To również jest temat, który nie pojawiał się nigdzie jeszcze rok temu. Oczywiście myśleliśmy o zwiększeniu produkcji samej Pilicy, ale był to wtedy produkt wyposażony tylko w bardzo krótki zasięg, obecnie otrzymać ma efektory większego zasięgu.
Czyli w zasadzie w ramach rozbudowanej Pilicy również powstaje taka Narew?
Powstaje rozwiązanie, które ma odciążyć Narew od realizacji zadań, które ten system może, aczkolwiek nie musi zwalczać.

Przemysł spodziewał się zamówień na kolejne baterie systemu przeciwlotniczego Pilica, ale w nowej Pilicy+ jest planowana jego rozbudowa poprzez implementację nowych efektorów, tym samym zapewnienie temu krajowemu rozwiązaniu nowych, rozbudowanych zdolności.
Dodam, w bardzo dużym stopniu stworzony przez polski przemysł. Można powiedzieć, że realizacja tego, o co przez lata walczyliście. Z polskiego przemysłu system dowodzenia, łączność, samochody, a od dostawcy zagranicznego bierzemy rakietę i wyrzutnię.
Realizuje się to, o czym kiedyś mówiliśmy w PGZ, ale też w MON, że tak powinny te programy wyglądać. Cieszę się, że udało się te koncepcje w końcu wdrożyć. „Mała Narew”, a szczególnie Pilica+, będą czymś rzeczywiście zbliżonym do wcześniejszych projektów. Efektora faktycznie nie mieliśmy, ale za chwilę będziemy w dużej mierze już go produkowali w liczbach tak dużych, że uzyskane technologie pozwolą nam na kolejny rozwój. I takie jest założenie.
Pytał Pan o dokonania z ostatniego roku. Na pewno udało się ułożyć pewne procesy i wprowadzić odpowiednie zasady funkcjonowania dla całej PGZ. Choćby w zakresie uproszczenia struktury, o czym ciągle też rozmawiamy, ale i przez wprowadzenie metod zarządzania, kumulacji obowiązków, czy pewnych procesów w ramach samej PGZ – chociażby integrację zakupów i obsługi prawnej. To wszystko organizacyjnie się udało i dalej postępuje. Widać tego efekty, bo to są oszczędności, jeśli chodzi o zasoby i czas. Chcemy, żeby zasoby w terenie skupiły się głównie na produkcji, realizacji projektów, formule którą określę jako fizyczną. To jest jeden aspekt. Drugi, to kwestia oszczędności czy możliwości dysponowania większym potencjałem, co daje też możliwości negocjacji z dużymi partnerami na innych zasadach niż pojedyncze spółki. I to jest również wymierny efekt. Myślę, że kolejne lata pokażą bardziej policzalne efekty tego kroku, który wykonaliśmy i sensownie realizujemy. Spójrzmy nawet na zakupy energii. Dzięki temu, że podjęliśmy odpowiednie działania rok temu, jeszcze przed skokowym wzrostem cen, mamy gwarantowane umowy dla całej Grupy i gwarantowane oszczędności z tego tytułu. Mamy dziś na rynku ceny energii nieosiągalne nawet dla przemysłu.
Przemysł zbrojeniowy jest bardzo energochłonny, od czego trudno uciec. Jest to dla was problem?
Wiadomo, że koszty produkcji będą rosły. Wynika to nie tylko ze wzrostu cen energii elektrycznej, czy gazu – bo on także służy do produkcji i ogrzewania. Wzrosły również koszty komponentów, części i samych materiałów. Przykładowo ceny stali nie pozostały bez zmian w stosunku do tych, które były jeszcze rok temu.
Biorąc po uwagę wzrost tych różnych czynników, czy możemy być jeszcze konkurencyjni wobec Zachodu?
Cały czas jesteśmy konkurencyjni. Na pytanie czy możemy być, odpowiem: musimy być konkurencyjni. Na pewno robimy wiele, żebyśmy dalej tacy byli.

Armatohaubica Krab jest symbolem polskich programów artyleryjskich. Pokazując bardzo dobre możliwości w trakcie działań bojowych w Ukrainie, system zyskał na zainteresowaniu i zamówieniu eksportowym. Grupa PGZ planuje zwiększenie zdolności produkcyjnych Kraba do blisko 100 dział rocznie.
Ten ostatni rok to również Pana kilkanaście miesięcy na stanowisku Prezesa Zarządu PGZ S.A. Patrząc na ostatnie kilka lat, stanowiska w resorcie obrony, w PGZ, trudno znaleźć bardziej doświadczoną osobę zajmującą się tym obszarem. Jaki ma Pan pomysł na przyszłość polskiej zbrojeniówki?
Rzeczywiście, ponad rok mojej obecności w PGZ to na pewno okres ciężkiej pracy. Czy jestem dziś najbardziej doświadczonym prezesem? Na pewno staram się wykorzystać każdy fragment mojej wiedzy i zaangażowania, aby przenieść PGZ na zupełnie inny poziom organizacyjny, bo rzeczywiście także z powodu wojny pojawia się dziejowa możliwość zwiększenia naszego potencjału przemysłowego. Wiele spółek przez ten okres odczuwa już poprawę, kilka na pewno musi zmienić swoją rzeczywistość. Przed nami są ciągle olbrzymie inwestycje. To nas nie ominie, ponieważ w wielu miejscach te inwestycje dotychczas w odpowiednio dużym tempie nie były realizowane, a wynikało to z tego, że potencjalne zamówienia i rynek był taki, jaki był. Z czego więc wynikało, że produkowaliśmy rocznie tylko kilkaset rakiet Piorun? Z tego, że takie były zamówienia. Ostatni rok to zintensyfikowanie naszej działalności nie tylko na rynku krajowym, ale też eksportowym. Z kilkoma sukcesami mogliście się państwo zapoznać. Przed nami jeszcze kilka innych tematów, które są dziś na różnym etapie realizacji. Nie wszystkie idą w tempie, którego byśmy oczekiwali. Dzieje się tak głównie z tego powodu, że w oferowanych przez nas produktach są elementy zależne od państw trzecich i nie zawsze to państwo jest zainteresowane, by pomóc nam w oferowaniu naszego kompleksowego produktu, bo czasami te kraje mają własny produkt konkurencyjny również na tym rynku. Staramy się w taki sposób zarządzać naszą organizacją i produktami, aby największa część tego know-how była rodzima i nie ograniczało to nas na kierunku eksportowym. Przykładem naszych problemów jest fińska Patria. Wieloletni alians Rosomaka z Patrią zaowocował tym, że Wojsko Polskie ma największą liczbę tego rodzaju pojazdów. Rosomak jest świetnym wozem, chwalonym przez żołnierzy…
…ale i już 20 lat produkowanym.
On między innymi jest taki świetny dlatego, że to nasi inżynierowie, nasi technicy i monterzy wykorzystali doświadczenia naszych żołnierzy z Afganistanu, które pozwoliły na wprowadzenie kilkuset zmian do tego pojazdu. Niestety, jest też tak, że te wszystkie nasze roboczogodziny nie przełożą się na własność intelektualną należącą do polskiego przemysłu. Forma umowy, która została w przeszłości zawarta i jest realizowana przez 20 lat w oparciu o pierwotny AMV, już się wyczerpała.
Ta umowa wkrótce się kończy.
Kończy się w 2023 roku. Mamy oczywiście przygotowaną wersję do aneksowania jej na kolejne kilka lat, ale warunki tego wynegocjowanego jakiś czas temu przedłużenia, dzisiaj nas w ogóle nie satysfakcjonują. Zwłaszcza, że Patria pokazała na kilku kierunkach eksportowych, że zupełnie nie podziela naszego przekonania.
Przewiduje Pan koniec Rosomaka na liniach produkcyjnych?
Oczywiście nie zniknie z wojska. Kwestie utrzymania, przebudowy, czy reorganizacji, mamy zabezpieczone drugą, bardziej długoterminową umową. Co zaś do dalszej produkcji, ja cały czas jestem optymistą i pozostaję otwarty na różne scenariusze. Nasi koledzy z Finlandii mają okazję zachować się biznesowo i partnersko, bo nie zamierzamy być petentem. To my dziś mamy potencjał produkcyjny. Nie przypominam sobie, żeby Finowie wyprodukowali taką liczbę jakiejkolwiek odmiany tego pojazdu na inne rynki. Choćby z tego powodu powinniśmy móc się porozumieć, bo stoją za tym pieniądze dla każdej ze stron, a zysk to zawsze najmniejszy wspólny mianownik. Jeżeli fińska strona tego nie widzi, my na siłę niczego nie będziemy robili. Mamy inne rozwiązania, mamy inne możliwości.
Powiedzmy zatem coś bliżej o tych alternatywach.
Myślę, że dla nikogo nie jest tajemnicą, że na paryskim salonie razem z partnerami z Korei Południowej podpisaliśmy porozumienie, które między innymi zakłada możliwą wspólną produkcję ich rozwiązania, wozu K808.

Dalsza produkcja pojazdów znanych pod marką Rosomak uzależniona jest od porozumienia z fińską firmą Patria. Grupa PGZ przygotowuje się również na rozwiązania alternatywne.
Niektórzy zastanawiają się, czy ten wóz to jest postęp.
Jest to trochę inna technologia, bo ten pojazd ma inne założenia, jeśli chodzi o podwozie, parametry jezdne, ma inną masę, a nawet materiały użyte do jego produkcji. Ale [K808] to jest wyjściowy temat. My rozmawiamy o nowej rzeczywistości i chęci przeniesienia tego transportera na inny poziom, jeśli chodzi o technologię i jego możliwości. Z Hyundai Rotem jesteśmy po wstępnych rozmowach o współpracy, bo dziś musimy tworzyć coś, co będzie skuteczne jutro. Może też to być współpraca w formie „PL”, czyli możemy zaproponować na tej bazie pewne własne rozwiązania, które będą nas bardziej satysfakcjonowały. Mamy też na stole cały czas możliwość zaprojektowania nowego wozu, wykorzystując nasze doświadczenia i inżynierów.
Są to realne zdolności? Rozumiem pakiet tych doświadczeń, propozycji, ale na ile w Pana ocenie jesteśmy w stanie przekuć to w materialny projekt przeprowadzony bez strategicznego partnera zagranicznego?
Mamy taką możliwość, bo dziś jesteśmy już w zupełnie innym miejscu.
Na ile są to marzenia Prezesa, a na ile realizm? Mam na myśli polski transporter, ale i wcześniej polski czołg.
Całkowicie nasza konstrukcja to jest kwestia czasu i zaangażowania pewnych środków. Przeliczaliśmy to już przy czołgu, gdy dwa lata temu rozpoczęliśmy taką analizę. Wtedy zaangażowałem do pracy całą lądową domenę ze wszystkich spółek, które mogłyby służyć do zbudowania całego potencjału dla czołgu. Dokonaliśmy analiz, obliczeń oraz weryfikacji naszego potencjału, czasu i możliwości w zależności od tego, co chcielibyśmy uzyskać i w oparciu o jakie rozwiązania. W najdłuższej perspektywie zakładaliśmy wybudowanie zupełnie nowego czołgu. Oczywiście do użycia przy zaprezentowaniu tej konstrukcji musielibyśmy się pokusić o zaprezentowanie pewnych elementów, które już są dostępne na rynku.
To jest w sumie naturalne. Koreańczycy akurat mają już dużo swoich komponentów, ale to by trwało wręcz dekady.
Przypominam, że nawet Amerykanie nie zaczęli od zera. Jakby nie było, protoplastą armaty Abramsa jest niemiecka „120-tka”. Korea też bazowała na zewnętrznych rozwiązaniach, Turcy też, nikt nie wyważa otwartych drzwi. Przy takim założeniu, my potrzebowalibyśmy około siedmiu lat, żeby gotowy i przetestowany pojazd przedstawić, ale mówię o całkowicie nowej konstrukcji. No i są pośrednie rozwiązania: skorzystanie z czegoś istniejącego, wspólna praca, wykorzystanie pewnych zdolności, potencjału naukowego i technologicznego. Samo zaprojektowanie na desce kreślarskiej kształtu, rozwiązań z wykorzystaniem mechanizmu armaty z lufą 120, a może kalibru 130 mm to nie jest znaczące wyzwanie. Będąc już przy projektowaniu, odpowiem na „zarzuty” o wzornictwie przemysłowym sprzętu wojskowego – pamiętajmy, że kształt jest nie tylko wizją twórcy, ale też bezpieczeństwem i wymaganym poziomem ochrony.
Nawet warto, aby stylista do takiego projektu przysiadł. Zeszliśmy jednak z tematu transportera, co z tym rozwiązaniem?
Ten projekt będzie zależał od tego, czego będzie oczekiwał zamawiający, którego zdanie jest najważniejsze. Wiemy, że jest jednak zainteresowanie projektem koreańskim. Pytanie, w jakim zakresie mamy ten pojazd dostosować, czego oczekuje wojsko, a co my możemy zaprojektować. Wiemy, co chcemy wdrożyć tam z naszych doświadczeń. Przykładowo, koreański wóz jest lżejszy, pewnie będzie potrzeba go trochę dociążyć…
…taka jest tendencja, wszystko staje się coraz cięższe, głównie z powodu opancerzenia…
… ale osłona balistyczna pojazdu to nie tylko pancerze, ale również i systemy aktywne. Nad ekwiwalentem trzeba się może zastanowić, bo im bardziej opancerzony wóz, tym jego produkcja jest droższa i samo użytkowanie staje się bardziej problematyczne. A czy zawsze uzyskamy oczekiwany efekt, patrząc na to co widzimy na Ukrainie? Niezależnie jaka to wersja czołgu, tak samo pali się po trafieniu przeciwpancernego pocisku. Pytanie, czy przy każdym uderzeniu przeżywa załoga, a ta jest przecież najważniejsza.

Zbudowane zdolności serwisowo-przemysłowe w obszarze wykorzystywanych już w Siłach Zbrojnych RP wozów bojowych (na zdjęciu Leopard 2A5), mają być skokowo wzmocnione dzięki współpracy z przemysłem Republiki Korei i takim produktom jak czołg K2.
Dużo trudniej o doświadczonych ludzi w każdym obszarze, od czołgistów, artylerzystów, po pracowników zbrojeniówki. Doświadczona kadra jest wszędzie na wagę złota.
W każdym z tych fragmentów, czy przy użytkowaniu, czy przy produkcji, najważniejszym elementem są wykwalifikowani ludzie. Na każdym stanowisku, od monterów, przez technologów, inżynierów, po kadrę kierowniczą, trzeba mieć wszędzie olbrzymią wiedzę i doświadczenie, aby realizować tak skomplikowane projekty. Na przykład Krab nie jest po prostu armatohaubicą, gdzie ładuje się ręcznie pociski i wstrzeliwuje je gdzieś w pole. Tak to nie działa. To dość skomplikowane urządzenie, naszpikowane elektroniką i systemami. Przy nowoczesnych projektach to już nie jest tylko spawanie.
Skoro już Pan nawiązał do tematu Kraba, kontynuujmy. Nie obawia się Pan, że są ryzyka związane z programem K9. Przez wiele lat uczyliśmy się Kraba, jak produkować, szukać możliwości modernizacji, maksymalnie polonizować, wojsko uczyło się go wykorzystywać. A trzeba to również podnosić, dla wojska nowy sprzęt to również ogromne wyzwanie, chodzi o organizację, chodzi o wystarczającą liczbę ludzi. Najczęściej się mówi, czemu przemysł tak mało dostarcza, a chyba z drugiej strony przemysł mógłby zapytać, kiedy po inwestycjach w zakład wojsko więcej będzie sprzętu odbierać. Takie są realia. Patrzę mogliwięc na plany K9, że wchodzimy w jakąś drugą odnogę i obawiam się, że znowu kolejne lata zajmie nam podnoszenie poziomu polonizacji, nauka tego systemu, poszukiwanie pola do jak najszerszego zastosowania własnych rozwiązań. Czy nie obawia się Pan, że przy Krabie zdobyliśmy już pewną bazę, wkrótce pewnie byłby i automat ładujący w ramach modernizacji, a pojawia się koreańska haubica, kolejne lata nauki, dreptania i może za 10 lat…
Huta Stalowa Wola jest producentem armatohaubicy Krab, która według danych w 90-95% jest produktem polskim, produkowanym w oparciu o zasoby Huty, naszych spółek i generalnie komponenty polskiej produkcji. Silnik jest oczywiście elementem, który pozyskiwany jest z zewnątrz, ale od tego się nie ucieknie. Kiedyś straciliśmy zdolności produkcji silników ciężkich w Polsce. To też jest temat dyskusji, czy teraz warto je odtwarzać. Ja myślę, że zawsze warto produkować w kraju jak najwięcej. Niemniej armatohaubica K9 jest to podobne rozwiązanie, oczywiście specyficzne w systemie załadunku amunicji. Z czego to wynika? Nasza armatohaubica opierała się o brytyjskie podejście, koreańska o amerykańskie, z dodatkowym wozem amunicyjnym. Więc zupełnie inaczej podeszli do tego konstruktorzy tych dwóch systemów, ale też armie, które stosowały tego rodzaju sprzęt.
Ja jestem zawsze optymistą i ze spokojem patrzę na jutro.. Po pierwsze, my w HSW mamy co robić. Huta ma wyprodukować jeszcze wiele armatohaubic Krab, bo to jest dziś nasze, rodzime rozwiązanie. Przypominam, że są też rynki zbytu, które musimy zaspokoić a są odbiorcy, którzy chcą dokładnie to rozwiązanie. Będziemy więc jednocześnie produkowali także armatohaubice K9 w aliansie z partnerami z Korei Południowej. Wspólnie będziemy przyglądali się, co można wykorzystać z jednego i z drugiego rozwiązania. Nasze armatohaubice mają przecież doświadczenie bojowe, które cały czas zbieramy i analizujemy. Za nimi stoi też doświadczenie naszych żołnierzy. Alians więc tych dwóch podmiotów i filozofii, w mojej ocenie może zaowocować tym, czego oczekuje się de facto od przemysłu, czyli skokiem do nowej, kolejnej wersji. Byłaby to kolejna faza prac nad armatohaubicą, w której wykorzystane zostaną wszystkie ciekawe rozwiązania – te nasze i te zapożyczone od Koreańczyków. Ale konfiguracja to jedno, podstawą jest zabezpieczenie produkcji dużych ilości sprzętu dla naszej armii. Myślę, że w sytuacji gdybyśmy nie byli w takiej geopolitycznej układance, nie byłoby konieczne podejmowanie pewnych decyzji zakupowych, moglibyśmy poradzić sobie z potrzebami zakupowymi sił zbrojnych. Dziś partnerstwo, jednoczesne wykorzystanie dwóch przemysłów, da nam korzyści w postaci większych dostaw sprzętu prowadzonych w tym samym czasie. Bo my w ramach PGZ również musimy rozpędzić produkcję samego Kraba do poziomu zbliżonego do 100 egzemplarzy rocznie. To jest kwestia fizycznej możliwości i odpowiedniego usytuowania takiej produkcji.
Na tych samych liniach w Stalowej Woli?
No właśnie nie tylko. Jedno to jest maksymalne zwiększenie produkcji w samej Hucie, ale i jej zdywersyfikowanie na innej linii produkcyjnej, a tym samym możliwość wytwarzania dodatkowej partii. Jakby udało się nam 48 Krabów robić w Hucie i drugie 48 na Śląsku – byłby to już zupełnie inny wolumen. Do tego dochodzą pozostałe części modułu Regina, wiele innych pojazdów, bo sprzedajemy ten sprzęt dywizjonami. Więc takie jest nasze główne zadanie. Poza tym musimy zaaplikować do PGZ zdolności produkcyjne dla armatohaubicy K9, w innym zakładzie, we współpracy z partnerem koreańskim. Ten temat obecnie znajduje się w trakcie analiz. Ostatnio przeprowadziliśmy z naszą całą domeną pancerną odpowiednie weryfikacje co do zdolności, liczby roboczogodzin, które jesteśmy w stanie absorbować na liniach produkcyjnych, w oparciu o to, ile takich roboczogodzin będzie potrzeba.

W kategorii pływających bojowych wozów piechoty priorytetem ma być Borsuk, obecnie przechodzący badania kwalifikacyjne. Pierwsze zamówienie pozyskano zaś w tym roku na system wieżowy ZSSW-30. Grupa PGZ również w przypadku Borsuka zakłada istotne zwiększenie zdolności produkcyjnych.
No i jak, jest przepaść?
Jest duża potrzeba zwiększenia naszego potencjału – czterokrotnie, a nawet pięciokrotnie.
Rozumiem, że dotyczy to różnych potrzeb, nie tylko związanych z K9. Haubica to jedno, a gdzie w tym wszystkim jest czołg K2?
Czołg to jest jeszcze jedna kwestia. Decyzja o wyborze platformy do budowy podstawowego czołgu zapadła poprzez podpisanie umów ramowych między Agencją Uzbrojenia a Hyundai Rotem. Za chwilę wchodzimy w etap umowy wykonawczej, jako ich producent w Polsce. A do tego musimy się przygotować, w zasadzie bardzo szybko, padały już terminy.
To są terminy szybsze niż koreańskie, a ich mam za naród dobrze zorganizowany.
Dlatego też będziemy korzystać z tego doświadczenia, bo oni mają taką linię produkcyjną już u siebie, mają też duże doświadczenia produkcyjne.
To oznacza zbudowanie takiej linii u nas?
Tak, mowa o zbudowaniu takiej linii u nas. Osiągnięcie efektu synergii to jednoczesna produkcja K2 tam i tu, żeby zwiększyć partie dostarczanego sprzętu. Chcąc wypełnić potrzeby sił zbrojnych, potrzeba zdolności produkcyjnych niczym z czasów II wojny światowej, ale wtedy technika pancerna była mało skomplikowana, a cała gospodarka była przestawiona na wojenne tory.
A teraz jest masa mikroelektroniki, z którą jest wszędzie problem.
K2 jest szczególnie naszpikowany dużą liczbą elektroniki, ma także automat ładowania, stąd też trzyosobowa załoga. Posiada systemy ostrzegania, wszędzie jest w nim elektronika, ale to też większe bezpieczeństwo dla załogi. Niewątpliwie jest to skomplikowane rozwiązanie i będziemy musieli na te potrzeby produkcyjne odpowiedzieć, i to nie tylko prostym składaniem korpusów. Docelowo, żeby to miało sens i jak największe korzyści, musimy przejąć jak najwięcej produkcji jego komponentów i elementów w Polsce, i zapewne będziemy to robili etapowo.
Ile faktycznie polskich komponentów będzie w K2, czy K9? W samolocie na pewno jak najmniej?
Samolot jest zaplanowany do zakupu jako gotowy. W ramach pierwszego pakietu produkcji u nas nie widzimy, bo to nie są też duże liczby. Pytanie, jaki byłby koszt pozyskania tych kompetencji i czy by się to opłacało.
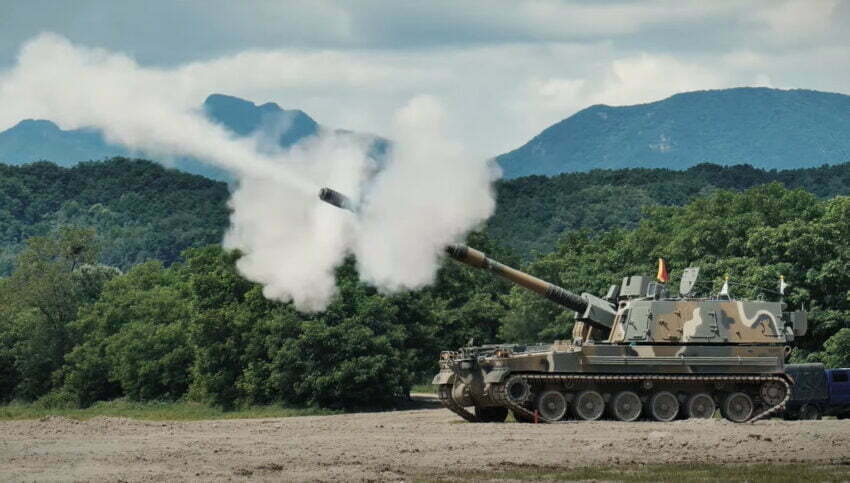
Zakup koreańskich haubic K9A1 ma być pierwszym krokiem do opracowania i wprowadzenia spolonizowanej wersji działa oznaczonej roboczo K9PL.
Jako prezes PGZ nie chciałby Pan w jednej z lotniczych spółek zobaczyć linii montażu końcowego FA-50? Myślałem, że to jest taki samolot, na który być może mamy takie ambicje?
My mamy bardzo daleko idące ambicje, ale na razie musimy odpowiedzieć na oczekiwania ze strony naszego rodzimego ministerstwa i wojska. Oni chcą sprzętu szybko i z powodu wojny jest to oczywiste. Nie ma więc co dyskutować, potrzebowalibyśmy więcej czasu niż obecnie producent tego samolotu, a tyle czasu my nie mamy.
Jest kilka zakładów lotniczych, a im również trzeba znaleźć przyszłościowe zajęcie, nowe produkty.
Zgadza się. Na początek będzie to pełny serwis samolotu FA-50 w Polsce na takim poziomie, jak robiliśmy to z MiG-29, czyli w zasadzie do gołej blachy. To już będzie ogromne wyzwanie, żeby utrzymać wszystkie te maszyny w szyku. Wiadomo, że nigdy nie ma 100% sprzętu gotowego do działań, zawsze są przeglądy i odpowiednio stosowane procedury serwisowe, ale to będzie i tak wyzwanie. Jednocześnie w Bydgoszczy będziemy serwisować samoloty F-16 należące do sił amerykańskich, a więc i tam tych samolotów będzie jeszcze więcej. Dodajmy do tego jeszcze nasze rodzime F-16 i wszystkie pozostałe samoloty, które są w dyspozycji naszych sił zbrojnych, a też tam są serwisowane. F-35 natomiast to jest już inna kwestia, więc tutaj musimy do tego inaczej podejść.
To na razie śpiew przyszłości.
To jest przed nami. Przypominam też, że obsługa Abramsa w zakresie spółek lotniczych też generuje pewne potrzeby. Silnik wykorzystywany w Abramsie zawiera elementy stosowane również w lotnictwie.
Czy ambicją jest, aby nasz WZL był od tych silników?
Dęblin prowadzi już pewne prace w tym zakresie z Honeywell, który jest producentem kluczowych elementów napędu do Abramsa. Mamy podpisane odpowiednie dokumenty, a czekamy na decyzje międzyrządowe.
Czy może większe nadzieje w lokowaniu zdolności zabezpieczenia eksploatacji są w partnerze koreańskim?
Chyba nie jest tajemnicą, że między innymi przemysł koreański postawił na olbrzymi rozwój rodzimych rozwiązań, dlatego, że miał kłopoty z pozyskiwaniem zdolności, czy kompetencji ze strony firm amerykańskich. My też ze współpracy z naszymi partnerami z Korei wyniesiemy olbrzymie doświadczenie, zdolności i kompetencje.
Jaki przyjmiemy model współpracy, może joint venture?
Nie wykluczamy takiego rozwiązania. Wpierw budujemy konsorcja, gdy będzie to robione, mechanizm ich tworzenia wyjdzie w trakcie działań. Myślę jednak, że forma joint venture byłaby dobrą formułą dla takiej współpracy. Byłoby ono łatwiejsze, jeśli chodzi o absorpcję do Polski wiedzy, która niekoniecznie w innej formule mogłaby być tanio i sprawnie przekazywana. Mimo entuzjazmu i otwartości naszych partnerów koreańskich, zdajemy sobie sprawę, że to też w pewien sposób musi być realizowane w oparciu o biznesowe przesłanki.
Z ich perspektywy również?
Z ich perspektywy również. Niemniej jednak, nie chodzi tylko o biznes w tym całym międzypaństwowym aliansie. To jest daleko idąca współpraca strategiczna. Proszę zauważyć, że mamy podobne obserwacje, podobne podejście do naszego sąsiedztwa i cały czas gotowość, bo to sąsiedztwo może być niestabilne.
Wracając do czołgu K2, jak Pan widzi tę produkcję?
Wielość projektów, które jednocześnie będziemy musieli prowadzić, spowoduje obłożenie naszego potencjału w całości. Wszyscy będą mieli tyle pracy, że oby tylko mieli możliwość jej przyjęcia. Co do decyzji ostatecznej, gdzie będziemy lokowali produkcję, podejmiemy ją wspólnie. Już takie rozmowy są prowadzone. Nieprawdą jest, że będzie jakiś konflikt na przykład z Bumarem. Być może niektórzy będą próbowali wytworzyć atmosferę problemu, ale nie będziemy absolutnie w ten sposób do tego podchodzili. Myślę, że Bumar, Rosomak i OBRUM będziemy musieli zaangażować na 200-300%. To nie jest tylko K9, nie jest tylko Borsuk, który też ma być produkowany rocznie w liczbach zbliżonych do setek egzemplarzy. Na 100-tysięczną armię było założenie, że będziemy potrzebowali około 1000 bwp, to ile ich potrzeba na armię 300-tysięczną, jak Pan myśli?

Pierwsza partia koreańskich czołgów K2 dla Polski ma liczyć 180 sztuk. Dostawy powinny być zrealizowane w latach 2022–2025.
Nie wiem ile Borsuków, bo zakładałem, że przybędzie może K21, a może coś z tzw. pustyni. Pan wierzy, że w takich ilościach to będzie Borsuk?
Podstawowym bojowym wozem piechoty w wersji lekkiej będzie Borsuk. Byłoby idealnie, jeżeli bylibyśmy w stanie wyprodukować ich dużo więcej niż 100 rocznie, a do tego zmierzamy. Rozsądnie patrząc na oczekiwania sił zbrojnych, jeżeli mielibyśmy dostarczyć np. 2000 Borsuków, to nie możemy tego robić przez 20 lat.
A gdzie wozy specjalistyczne?
Wszystkie z naszych zakładów będą więc miały dużo pracy. Musimy to dobrze zaplanować i to nie jest kwestia historii lokalizacji, czy historii produkcji. To jest kwestia zdolności, możliwości pozyskiwania ludzi, bo tego posiadanego dziś personelu będzie trochę mało. Więc potrzeba nam znaleźć wykwalifikowanych pracowników. Logistyka też jest niezbędna w tej rzeczywistości.
Widzę to jako system zdecentralizowanej produkcji, gdzie w procesie uczestniczyć będzie wiele zakładów.
Wszędzie tam, gdzie to będzie miało uzasadnienie pod względem kosztów i logistyki, będzie to zdecentralizowane, gdzie rzeczywiście na poczet jednego produktu będzie wiele składowych elementów. Docelowo musimy się skupić na ulokowaniu konkretnych rozwiązań w danych lokalizacjach, żeby mieć pewność ostatecznego ich zrealizowania. Spójrzmy na zdolność do produkcji luf w Hucie, gdzie proces ten był przygotowany do poziomu bieżących dostaw. Oczywiście HSW podjęła już decyzje inwestycyjne, przy naszym wsparciu, już w zeszłym roku zostały zamówione kolejne urządzenia i maszyny. Huta już posiada projekty na zwiększenie swoich mocy produkcyjnych, w zakresie produkcji luf, ale nie tylko. Pytanie, czy przy takiej skali przedsięwzięć tylko HSW ma się zajmować produkcją luf? Czy nie powinniśmy przenieść części tej produkcji, albo zduplikować wytwarzanie luf w innym zakładzie. Może i na Śląsku, kiedyś w Bumarze była lufownia.
A co z napędami?
Już niebawem z partnerami koreańskimi odpowiemy na to pytanie, bo także zostało ono postawione. Pojawia się w dyskusji ulokowanie u nas montowni silników, a potem na tyle, na ile będziemy mogli zaabsorbować i na ile będzie nam pozwalała współpraca z partnerami, umieścić i produkcję komponentów w Polsce. Uwzględniając, że taki sam silnik jest w Krabie, w K9 i w bwp K21 i biorąc pod uwagę oczekiwania sił zbrojnych oraz nasze ambicje eksportowe, to ulokowanie takiej montowni w Polsce jest niezbędne.
Skąd wziąć pieniądze, żeby postawić te wszystkie zakłady?
Środki częściowo zawsze są zapisane w kontraktach. Są również środki inwestycyjne, o które występujemy do Skarbu Państwa w ramach dokapitalizowania PGZ. Mamy też i różne inne mechanizmy oraz instrumenty finansowe, jak na przykład kredyty.
Mówimy o miliardach złotych?
Mówimy o kilku miliardach złotych w perspektywie kilku lat.
Kwota z perspektywy wartości programu zbrojeń nie jest jakimś szokiem.
Nie jest szokiem, bo to nie jest budowanie od podstaw. Faktycznie chodzi o rozbudowanie obecnych zdolności. Nikt dziś nie jest w stanie rozbudować swoich zdolności produkcyjnych ot tak. Nawet partnerzy zagraniczni, przy zwiększonych zamówieniach w ostatnich miesiącach jasno deklarują, że terminy dostaw są dużo bardziej odległe niż przy standardowym poziomie zamówień. Wynika to z tego, że nie da się w prosty sposób odkręcić mocniej kurka z produkcją choćby amunicji.

Polskie produkty artyleryjskie to nie tylko haubice Krab i moździerze Rak, ale tak ważna amunicja kierowana do nich. Widoczny na zdjęciu pocisk APR-155 jest już w praktyce gotowy do produkcji.
Przy okazji Pana słów, nie jest dla nikogo tajemnicą, że w Polsce nawet w tych podstawowych sprawach jak proch czy niektóre rodzaje amunicji, utraciliśmy krajowe zdolności do ich produkcji. Jak to wygląda?
Wiele lat traktowania sił zbrojnych jak przysłowiowe piąte koło u wozu owocowało podejściem do przemysłu zbrojeniowego, które zakładało, że wiele rzeczy w ogóle nie będzie nam potrzebnych. Między innymi w ten sposób została zlikwidowana, a konkretnie zezłomowana, linia produkcyjna nitrocelulozy w Mesko. Dziś, ci którzy podjęli te decyzje krzyczą, dlaczego my nie produkujemy niektórych rodzajów amunicji. Właśnie przez takie decyzje sprzed lat.
Możemy to odkręcić?
Nie są to decyzje nieodwracalne, ponieważ dwa lata temu podjęliśmy wspólny trud o uzyskanie dodatkowego dokapitalizowania dedykowanego do odtworzenia produkcji w Mesko, między innymi amunicji małokalibrowej, średniokalibrowej i prochów dwu i wielobazowych oraz do częściowego pozyskania zdolności w zakresie produkcji nitrocelulozy. Jesteśmy w trakcie tej inwestycji. Prawdą też jest, że nikt w zasadzie z producentów amunicji na świecie nie jest w 100% samowystarczalny. My musimy zadbać o to żebyśmy byli gotowi do produkcji tych komponentów, z którymi możemy mieć problem w przypadku, gdy będziemy musieli tę produkcję gwałtownie zwiększyć, produkować np. na potrzeby czasu „W”. W Mesko toczą się duże inwestycje, wszystko po to właśnie, abyśmy w jak największym stopniu te nasze zdolności odbudowali, ale też się uniezależnili. Już za chwilę będziemy otwierali nową halę w Mesko, która będzie wyposażona w linię produkcyjną amunicji mało- i średniokalibrowej. Również na tych już istniejących liniach zostało zaimplementowanych wiele nowych maszyn, urządzeń, które też już pracują.
Mówiąc krótko, ta typowa amunicja powinna się szybciej pojawić w wojskowych magazynach w dużo większych ilościach.
Będzie ona też tańsza, chociaż dzisiaj trudno odnosić się do jakichś cen. Te sprzed roku nie są już nigdzie wyjściowymi. Relatywnie będzie tańsza proporcjonalnie do tego, co mogliśmy oferować obecnie. Skupimy się na utrzymaniu potencjału w tych produktach, które dla naszych sił zbrojnych będą najważniejsze. Wojsko też musi się określić, które rodzaje amunicji, które kalibry, chciałoby dalej pozyskiwać, a z których możemy zrezygnować. Wynika to z tego, w jaki gwałtowny sposób wojsko niektóre z nich wycofało ze swoich zasobów.
Niektóre sprawy ze sprzętem posowieckim same się w ostatnich miesiącach wyjaśniły.
Chociaż nie zamykamy drogi do tego, że partnerzy zagraniczni mogą chcieć pozyskiwać te kalibry. Nie wyrzucamy tego do kosza.
No właśnie, jeśli chodzi o potrzeby ukraińskie, jak to wygląda w przypadku PGZ?
Jesteśmy w stałym kontakcie z partnerem ukraińskim, toczą się rozmowy na różnych poziomach: międzyzakładowych, technicznych, centralnych. Mamy z Ukroboronprom podpisane odpowiednie porozumienia. Wkrótce te rozmowy skończą się podpisaniem umów w takich obszarach jak np. remonty czołgów. Dziś kilka naszych spółek prowadzi również produkcję komponentów na rynek ukraiński, dla ich zakładów, bo niektóre kompetencje u naszego sąsiada stracono. Trzeba przy tym pamiętać, że Ukraina także walczy, żeby jak najwięcej zrobić u siebie. Tylko tego, czego nie jest w stanie robić sama, przekazuje dalej i głównie są to serwisy wyższego stopnia i produkcja. Rozpoczniemy też wspólną produkcję ich pojazdów bojowych. To wszystko powoli nabiera kształtu.
Gdzie chcemy produkować ukraińskie wozy?
Jeszcze nie chciałbym tego przesądzać. Mamy dla nich przygotowane trzy lokalizacje i wszystkie się Ukraińcom podobają, czekamy tylko na ostateczną zgodę. Na pewno w jednym miejscu będzie produkcja, a w innym wyposażanie. Nie będziemy w 100% robili tych wozów, tylko wyposażone podwozia będą stamtąd wyjeżdżały.

W grupie krajowych nowych rozwiązań, które zapewne wkrótce trafić mogą do polskiej armii, znajduje się pojazd minowania narzutowego Baobab-K.
Funkcjonowanie przemysłu w czasie wojny to ciekawy i dziś szczególnie aktualny temat. Wojna rosyjsko-ukraińska dla nas to również duża nauka. Jakie ma Pan spostrzeżenia, co robić z naszym przemysłem, jak go chronić?
Mają w Ukrainie problem, którego my chcemy uniknąć. Między innymi poprzez dywersyfikację i przenoszenie produkcji albo jej powielanie w kilku lokalizacjach. Właśnie dlatego w pewnym momencie Ukraina zaprzestała produkcji niektórych rozwiązań, ponieważ mieli scentralizowane, duże zakłady w jednym miejscu, po części, jak my dziś. Likwidacja możliwości produkcyjnych poprzez atak na jeden z tych zakładów, kompleksowo zamykała zdolność do produkcji. Dlatego chcemy zbudować i umożliwić produkcję naszych, różnych rozwiązań, w zachodniej części kraju, żeby uniknąć jednorazowego, gwałtownego wyłączenia zdolności produkcyjnych, jeżeli doszłoby do napaści na Polskę. Dwa łańcuchy dostaw to jeden z takich elementów.
Pandemia już pokazała, gdzie są słabe strony naszego systemu, i już wtedy zareagowaliśmy. My dziś nie jesteśmy w stanie wojny, nie mamy zastosowanych specjalnych procedur do przestawienia się na produkcję wojenną, ale mamy już doświadczenia pokazujące, co będzie potrzebne, w jakiej formie możemy współpracować w sytuacji, gdy doszło do zagrożenia naszej granicy na odcinku białoruskim, do próby nielegalnego przerzucania tzw. emigrantów na stronę polską. Komasacja naszych służb na tym obszarze, potrzeby ochrony granicy nie tylko przez Straż Graniczną, już wtedy pozwoliły nam zaobserwować pewne potrzeby i podjąć decyzje co do zwiększania produkcji. Do bardziej elastycznego podejścia do współpracy z instytucjami państwowymi, zatowarowania wszędzie tam, gdzie to było możliwe, odtworzenia niektórych kompetencji, choćby produkcji tarcz, których jakiś czas już nie robiliśmy.
Tarcz?
Tarcz dla policji. Nie robiliśmy ich, bo nie było takiej potrzeby. Sytuacja pokazała, że musimy się przygotować na niestandardowe rozwiązania, mimo tego, że nie jesteśmy w stanie wojny. Obserwacja tego, co się dzieje w Ukrainie owocuje decyzjami, które będą już wkrótce widoczne.
Chciałem zapytać także o program Tytan. Czy jest jakiś pomysł, żeby nie czekać do jego finalizacji, bo to może nigdy nie mieć miejsca, a wprowadzić stosowną procedurę dla wdrożenia tych elementów, które powstały, na które ktoś w wojsku czeka?
Prowadzimy dialog z zamawiającym na temat innej metody wprowadzenia Tytana nie tylko jako cała, zamknięta praca. Wiemy wszyscy, że MSBS Grot, czy pistolet VIS-100, to wdrożone elementy z tej pracy. Zmierzamy do tego, aby jak najwięcej tych elementów trafiło do Sił Zbrojnych, bo czas działa na niekorzyść dla różnego rodzaju rozwiązań. Kilka lat temu było to nowatorskie, kompleksowe wyposażenie żołnierza, z systemami elektronicznymi, śledzącymi, czy nadzorującymi parametry życiowe. Dziś technologia bardzo szybko idzie do przodu, szczególnie w zakresie elektroniki, co pokazuje, że powinniśmy szybko wdrażać i zastanawiać się już nad Tytanem 2.0. To by wymagało dalszego technologicznego skoku, jeśli chodzi o rozwiązania. Czekamy na uzgodnienie takiego modelu współpracy, zamawiający jest otwarty, co też jest olbrzymim postępem.
A z przeciwpancernym Piratem co się dzieje? Jesteście zainteresowani także pociskiem Moskit?
Powinniśmy zamknąć temat w sensie pozytywnym. Pirat będzie produkowany. Moskitem też jesteśmy zainteresowani. Widzimy przyszłość w tym projekcie. Oczywiście będziemy rozwijali i każdą inną współpracę z naszymi partnerami w podobnych rozwiązaniach, w każdym zakresie, w jakim będą oczekiwały od nas Siły Zbrojne.
Na koniec, Panie Prezesie, o czym będziemy rozmawiać za rok?
O tym, że dostarczyliśmy „małą Narew”, że trwa produkcja niszczycieli czołgów, rusza produkcja seryjna Borsuka, że trwa proces inwestycyjny pod nowe linie produkcyjne na zachodzie naszego kraju bądź innej lokalizacji pod czołg K2, że rekrutujemy ludzi i że Miecznik jest na etapie produkcyjnym, a jeszcze będzie zapewne i Baobab i kilkanaście innych przedsięwzięć. Jak Pan widzi, plany są ogromne, jest też u nas entuzjazm, by tym wyzwaniom sprostać.
Dziękuję za rozmowę.